Feb . 17, 2025 22:20
Understanding the dimensions and features of a 150 flanged ball valve is crucial for professionals who operate in industries such as oil and gas, chemical processing, water treatment, and manufacturing. As experts, we explore these components through experience and authoritative insights, ensuring you get a comprehensive view of why the dimensions of these valves are a key consideration in industrial applications.
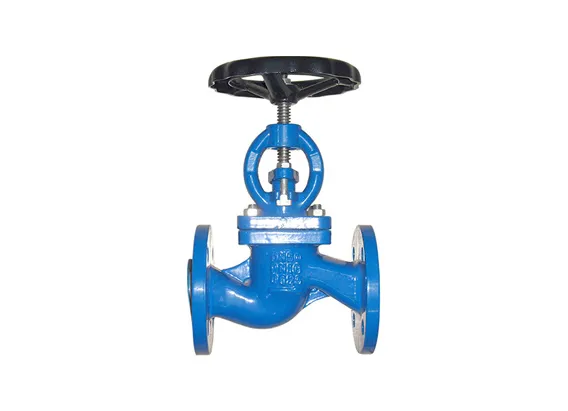
In the realm of industrial plumbing and fluid control systems, a flanged ball valve functions as an efficient shut-off valve that offers superior sealing capabilities. The “150” refers to the pressure rating in pounds per square inch (PSI), also known as Class 150. This rating indicates the valve's ability to withstand moderate pressure, making it ideal for a variety of applications where reliable sealing and ease of operation are essential.
I have spent over two decades working with various valve specifications, and the significance of dimensions cannot be overstated. Critical to the ball valve's effective selection and installation are aspects like face-to-face dimensions, flange diameters, and bolt circle diameters, as defined by ANSI B16.
10 standards. These standards ensure uniformity in the production and application across different manufacturers, thereby enhancing compatibility and reliability in design.
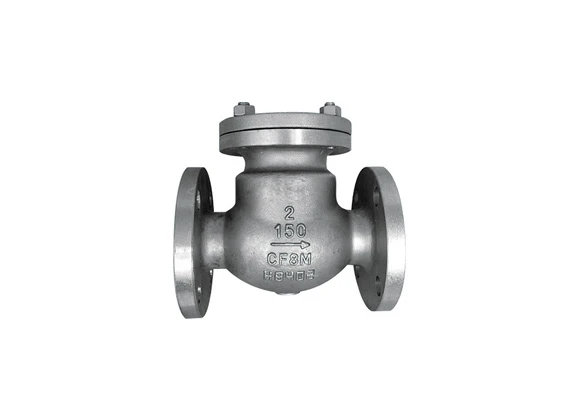
Face-to-face dimension is one of the most critical in gauging the suitability of a 150 flanged ball valve within a system. Specifically, the face-to-face dimensions determine the space taken up by a valve when placed in its intended pipeline. Ensuring these measurements are accurate is vital for proper installation and functionality, as even minor deviations can lead to inefficiencies or system failures. Industry professionals often rely on precise measurements to align upstream and downstream piping accurately.
The flange diameter and the bolt circle diameter are equally significant. Flange diameters must match precisely with adjacent components to prevent leaks and coordinate alignment. Typically, these valves come in various standard sizes, with flange diameters ranging widely, thus accommodating different pipes and functional requirements. The industry’s confidence in these dimensions comes from both historical domain knowledge and the rigor of multiple tests validating their resilience under operating conditions.
150 flanged ball valve dimensions
Furthermore, expertise in this field acknowledges that a balance between the valve size and flow control is necessary. A larger valve might suggest higher flow capacity, but system requirements dictate the appropriate choice. Engineers must assess various factors such as fluid type, pressure, and temperature to ensure the optimal valve is deployed, considering not just immediate needs but long-term operational efficiencies and safety.
Accountability in selecting ball valves extends to understanding the materials used. Typically, Class 150 flanged ball valves are manufactured from stainless steel or carbon steel, with the former offering superior corrosion resistance and longevity. The metallurgy plays a pivotal role in the valve's performance, especially in aggressive environments. Trust in the material’s integrity comes from extensive field data and certifications that reassess quality across various conditions.
Another cardinal point in the selection process is the aspect of maintenance. A well-chosen ball valve must provide ease of access for servicing, requiring minimal downtime. From my extensive experience, I advise that the inherent simplicity of a ball valve’s function—open or close—should translate to an equally straightforward maintenance protocol. Thus, predictive maintenance techniques and regular inspections are highly recommended to preclude potential failures.
Certifications from reputable quality assurance organizations further bolster the trustworthiness of these products. Organizations like API and ISO ensure that the manufacturing and performance of these valves meet international quality standards, thus promoting safety and reliability.
In sum, truly mastering the use of a class 150 flanged ball valve involves an intricate knowledge of its dimensions, material quality, and application-specific considerations. Drawing on the wealth of experience across multiple industry contexts ensure that your fluid systems operate under the best conditions possible, enhancing both efficiency and safety. As we leverage equipment that must stand up to demanding environments and rigorous expectations, understanding and utilizing these dimensional standards effectively is invaluable.