Feb . 16, 2025 16:32
Ball valves with flanges are integral components in a wide range of industrial applications. These valves are designed to regulate the flow of a medium—such as liquid, gas, or steam—through a series of pipes in a systematic and controlled manner. The simplicity of their design, coupled with their operational efficiency, makes them indispensable for industries like oil and gas, manufacturing, water treatment, chemical processing, and more.
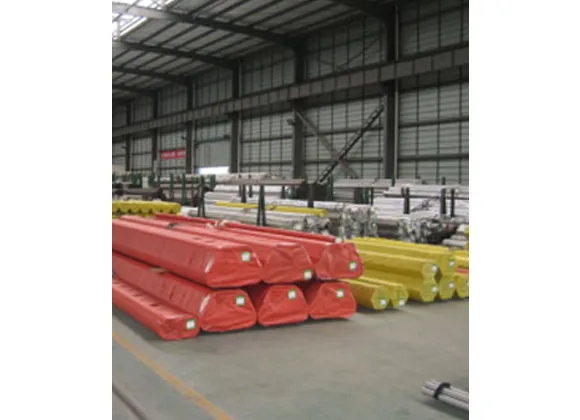
In terms of expertise, understanding the role of a ball valve with flange begins with its construction. These valves consist of a hollow, perforated, and pivoting ball that is used to control flow.
The ball is housed inside a valve body and connected through flanges to pipes. The flanges are plate-like structures that protrude out and allow the valve to be bolted to other components in the system, ensuring stability and reducing the risk of leaks. This crucial feature not only supports the valve during operation but also simplifies maintenance and replacement procedures.
From an authority perspective, the reliability of ball valves with flanges cannot be overstated. They provide dependable performance in high-pressure and high-temperature environments, which is why they are the preferred choice for critical applications. Additionally, manufacturers adhere to strict standards and certifications, such as API, ANSI, and ISO, ensuring that these valves meet the rigorous demands of various industries.
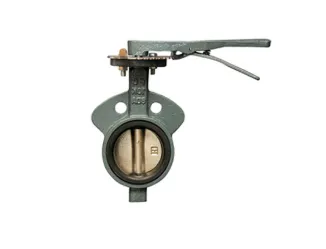
The trustworthiness of flange-connected ball valves stems from their proven track record in providing leak-proof service. Their design minimizes the likelihood of leaks even after repeated cycles of operation, thanks to the tight seal formed between the flanged connections and the ball when the valve is in the closed position. This efficiency in sealing reduces operational hazards, particularly in scenarios involving hazardous or volatile materials.
ball valve with flange
Experience has shown that the maintenance of ball valves with flanges is relatively straightforward, contributing to their long-term operational viability. Most flanged ball valves feature a full-bore design, allowing for easy passage of cleaning equipment during maintenance activities. This design minimizes pressure drop and enables the smooth flow of media, reducing wear and extending the life of both the valve and the connected piping system.
In specific applications, the choice of material for ball valves with flanges can significantly impact their performance and longevity. Stainless steel is often favored for its resistance to corrosion and ability to withstand extreme temperatures. For industries where purity of media is essential, such as food and beverage or pharmaceuticals, these valves may also incorporate special coatings or treatments that adhere to stringent sanitary standards.
Moreover, innovation in valve technology is taking these essential components to new heights. Automated flange ball valves, equipped with electric or pneumatic actuators, allow for remote monitoring and control, enhancing both safety and efficiency. This capability is especially beneficial in large installations where manual operation would be impractical or time-consuming.
To sum up, ball valves with flanges are more than just components in an industrial setting; they are pivotal to the seamless operation of complex systems. Their design, material composition, and adherence to industry standards ensure performance that can be counted on under the most demanding conditions. Choosing the right valve entails not just understanding the application requirements but also factoring in future needs such as automation and connectivity, making these valves a sound investment for companies dedicated to optimal performance and safety in their operations.