Feb . 10, 2025 11:42
Butterfly valves have long been pivotal in myriad industrial applications, and understanding the nuances of their sizes is integral for optimal performance. Selecting the right butterfly valve size involves expertise and a comprehensive grasp of specific system requirements. This article aims to elucidate the intricacies involved in choosing the appropriate butterfly valve size, enhancing operational efficiency while ensuring reliability.
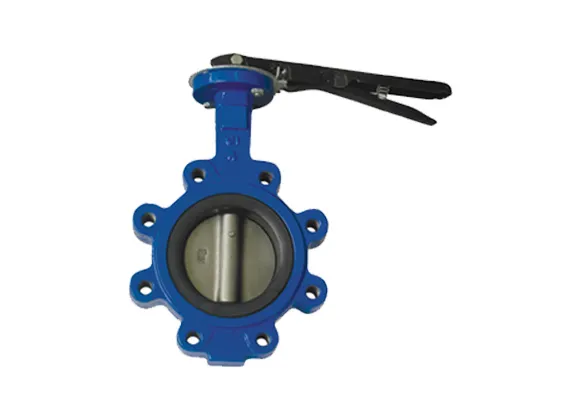
When engineers or procurement specialists embark on selecting butterfly valves, they must consider various factors, such as fluid type, pressure requirements, flow characteristics, and installation constraints. The valve size directly influences these elements, making it crucial to hone in on the precise specifications needed for your application.
Butterfly valves are typically measured and categorized by the diameter of the pipe they will be installed into. Sizes can range from small diameters suitable for precise applications to larger sizes necessary for substantial industrial processes such as water treatment, chemical processing, and oil and gas management. Understanding the application's operational parameters is the first step in choosing the correct valve size.
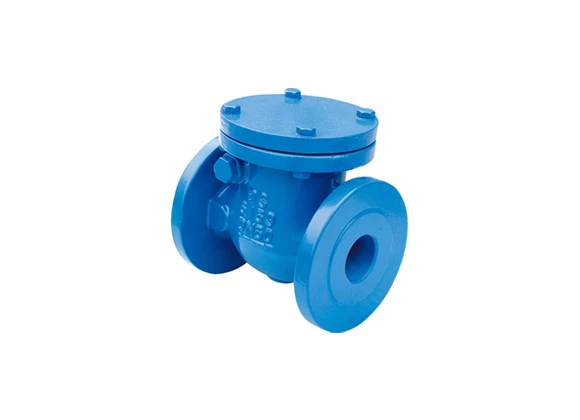
Pressure ratings and flow velocity are vital factors in determining the right butterfly valve size. Each valve size is designed to withstand specific pressure levels and flow rates without compromising performance. Using a valve that's too small might create unnecessary pressure drops, while an overly large valve can lead to inefficient flow control and potential cavitation issues. Professionals often use standardized charts that correlate valve sizes with pressure ratings and flow capacities to make an informed decision.
The choice of material also plays a pivotal role and is intrinsically linked to valve sizing. Common materials for butterfly valves include stainless steel, cast iron, and PVC, each offering distinct properties that affect the valve's overall footprint and suitability for different environments. For instance, stainless steel valves generally permit higher pressure tolerances and temperatures compared to PVC, which might have sizing implications based on the application's environmental conditions.
butterfly valve sizes
Moreover, the type of actuator, whether manual, pneumatic, hydraulic, or electric, influences the selection of valve size. The actuator must be compatible with the valve size to provide adequate control and ensure system responsiveness. This compatibility guarantees a seamless integration into the system and avoids operational inefficiencies.
Furthermore, lifecycle considerations should not be overlooked. Selecting an appropriately sized butterfly valve can significantly impact maintenance schedules and operational longevity. A well-sized valve reduces wear and tear, extending its service life and minimizing downtime, which translates to reduced operational costs over time. It is crucial for experts to assess the Total Cost of Ownership (TCO) when determining the optimal butterfly valve size.
Installation space is another consideration that, if neglected, can create operational challenges. The physical size of the valve, particularly in tight installations, can affect ease of access for maintenance and can necessitate piping modifications. Therefore, it's essential to consider the valve's spatial dimensions when determining suitability for a particular setup.
Lastly, regulations and standards like the American National Standards Institute (ANSI) or the International Organization for Standardization (ISO) provide guidelines that can influence valve size selection. These standards ensure that the valve fits into an industry-accepted framework for safety and performance, offering an additional layer of reassurance regarding the valve's reliability and efficiency.
In conclusion, selecting the correct butterfly valve size involves a detailed assessment of operational demands, environmental conditions, material compatibility, and regulatory standards. Expertise in understanding these factors and how they interact helps professionals choose a valve that ensures optimum performance, operational reliability, and longevity. By focusing on informed decision-making and adhering to industry standards, organizations can leverage butterfly valves for enhanced system performance and efficiencies across various applications.