Feb . 14, 2025 11:21
Butterfly valves with tamper switches play a crucial role in industrial and commercial applications, serving as a key component in fluid control and safety systems. These valves are valued not only for their efficiency and reliability in regulating flow but also for their integration with tamper switches, which significantly enhance safety and operational oversight.
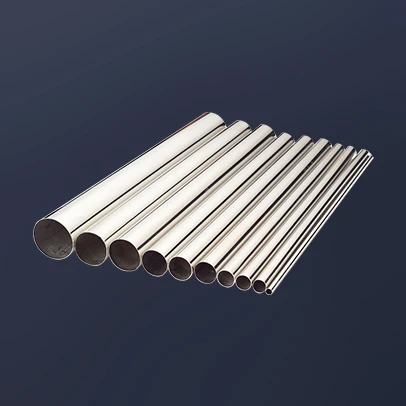
Butterfly valves are radial flow devices known for their efficiency in piping systems. They operate through a rotating disc, which acts as the closing mechanism. When the disc is rotated a quarter turn, it allows for flow through the pipe; a similar turn in the opposite direction blocks the flow. This simple but effective mechanism makes butterfly valves an ideal choice for managing large volumes of liquid or gas.
One of the standout features of modern butterfly valves is the integration of tamper switches, which elevate their functionality and safety. Tamper switches are designed to detect unauthorized interference, providing real-time alerts when the valve’s position is altered outside authorized operational requirements. This feature is vital in industries where precise flow control is essential, such as chemical processing, water treatment, and energy production.
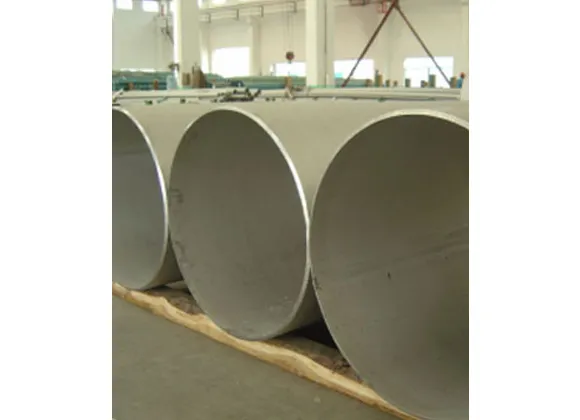
The expertise behind the design of butterfly valves with tamper switches lies in their engineering. The valve body must accommodate the switch without sacrificing durability or performance. High-grade materials, like stainless steel or hi-tech polymers, are often used to ensure the valve can withstand harsh environments and corrosive substances. Additionally, the integration of tamper switches requires sophisticated electronics, usually involving sensors that monitor valve position with high accuracy.
For organizations that prioritize operational safety and efficiency, the authority of using butterfly valves with tamper switches cannot be overstated. Dependable valve operation is vital in preventing leaks and spills, which could not only disrupt operations but also pose environmental hazards. In fire protection systems, for example, the tamper switch ensures that the valve remains in its intended position, either fully open or closed, to guarantee a quick response during emergencies.
butterfly valve with tamper switch
Trust is a crucial factor in deploying these valves within critical systems. Manufacturers ensure that each valve undergoes rigorous testing to meet industry standards. Certifications from leading standards organizations, such as the American National Standards Institute (ANSI) or the International Organization for Standardization (ISO), provide additional assurance of the product's reliability and performance.
Operators who have experience with butterfly valves equipped with tamper switches often appreciate their dual function. Not only do they provide efficient flow control, but the added layer of security from tamper monitoring instills confidence that the system is safeguarded against unauthorized adjustments. This peace of mind is invaluable in operations where precision and safety are paramount.
Additionally, the adaptability of butterfly valves with tamper switches makes them suitable for retrofitting older systems. Their compact design and ease of installation allow for minimal downtime, which is a significant advantage in busy industrial environments. The ability to integrate seamlessly with existing control systems via simple interfaces enhances their appeal as a modern solution for fluid management.
For facilities managers and engineers, selecting a butterfly valve with a tamper switch involves assessing the specific needs of their system, including pressure range, material compatibility, and the required level of automation. Consulting with experienced suppliers who understand the nuances of these applications is recommended to ensure the optimal fit.
In summary, butterfly valves equipped with tamper switches represent a confluence of mechanical efficiency and modern safety features. They exemplify the advancements in fluid control technology, meeting the ever-growing demands for safety, reliability, and precision in critical industrial and commercial systems. As more industries recognize the benefits these innovative valves provide, their implementation will likely become a standard practice in operations concerned with both efficiency and security.