Feb . 15, 2025 22:57
Flange checks are an essential part of maintaining the integrity and performance of various mechanical systems. A flange, a critical component in pipe systems, connects pipes, valves, pumps, and other equipment to form a sealed system. To ensure optimal safety and functionality, regular flange check procedures must be followed.
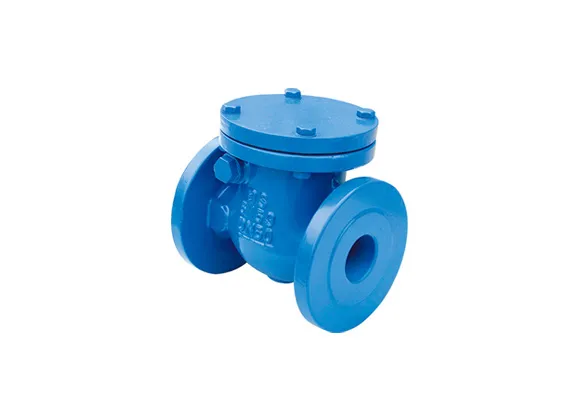
Achieving a foolproof flange check process requires a deep understanding of both the theoretical and practical aspects of flange connections. For any industry professional looking to enhance their expertise in this area, experience with various flange types and materials is crucial. There are several flange types such as slip-on, weld neck, socket weld, lap joint, threaded, and blind flanges each serving a unique purpose based on the system’s requirements.
Carrying out a flange check begins with a detailed inspection procedure, primarily focused on identifying signs of wear, corrosion, or damage. Flanges are typically made from stainless steel, carbon steel, cast iron, aluminum, brass, or bronze, each material offering different durability and resistance to elements. Thus, expertise in materials science can guide decisions on the appropriate maintenance or replacement strategy during a flange check.
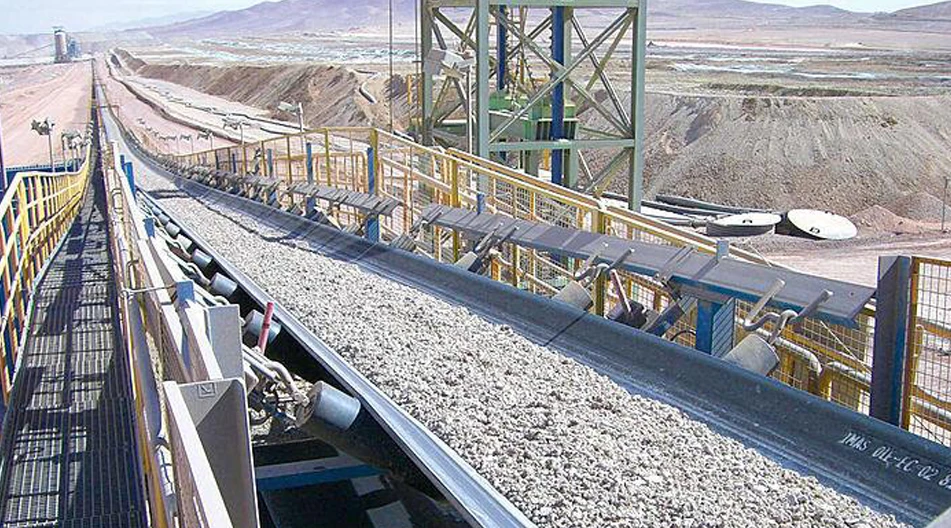
The procedure must be thorough yet methodical. It involves a close inspection of gaskets, bolts, and the flange face for signs of leakage or stress. The presence of rust or unusual vibrations could indicate a compromised seal, necessitating an immediate response to prevent potential operational failures. Utilizing advanced non-destructive testing methods like ultrasonic testing, radiographic testing, or magnetic particle testing provides a non-invasive means to evaluate the condition of the flanges without dismantling the system.
Precision in checking the torque settings on flange bolts is another vital part of the process. Tightening sequence and specifications should align with the manufacturer's instructions to ensure the flange's integrity. Regular training and certification in bolt tensioning methods are vital for professionals conducting these checks.
flange check
Authoritative guidelines from international standards such as ASME B16.5 or industry best practices should inform the flange check procedures. Following these standards not only enhances the credibility of the inspection but ensures compliance with global safety norms.
Building trust, particularly in systems for critical industries such as oil and gas, pharmaceuticals, and chemical manufacturing, hinges on meticulous documentation of inspection results. Recording the findings, including photographic evidence of the flanges, pressure tests, and maintenance activities, supports future assessments and planning for systematic upkeep.
Leveraging automation tools and IoT-enabled devices can further streamline flange checks. These technologies offer real-time monitoring and data analytics capabilities, providing valuable insights into the system's performance, ultimately optimizing the flange maintenance regime.
A successful flange check program combines frontline technical expertise with strategic oversight and digital innovation. Implementing a continuous improvement cycle in maintenance operations is fundamental for extending the life of flange systems, minimizing unplanned downtime, and ensuring safety and efficiency across industrial operations.
Lastly, collaborating with recognized industry experts and thought leaders can enhance understanding and execution of flange checks, encouraging knowledge exchange and sharing of best practices across the professional community, thereby solidifying the company's reputation as a responsible and informed entity in its field.