Feb . 13, 2025 18:57
Wafer and lugged butterfly valves are pivotal components in various industries like water treatment, oil and gas, and food processing. Understanding their unique features, applications, and advantages can significantly impact system performance and efficiency.
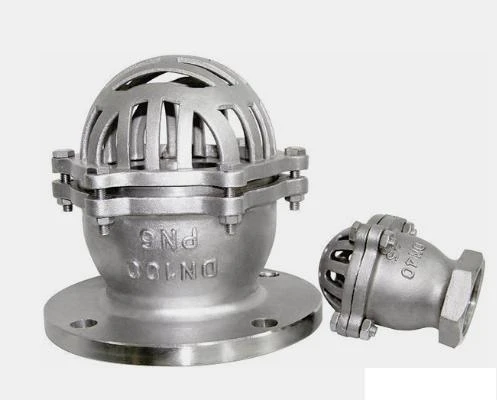
Butterfly valves, characterized by their rotating disk mechanism, are renowned for their ability to regulate flow. Their design simplicity offers several benefits, including low maintenance, ease of installation, and cost-effectiveness. Within the butterfly valve category, wafer and lugged designs stand out due to their distinct construction and application benefits.
The wafer butterfly valve is lauded for its compactness and lightweight nature. Engineered to fit between two flanges, it’s held in place by bolts that pass through the flanges and valve body. This design minimizes space requirements, making it ideal for systems where compact installation is crucial. Its simplicity extends to its cost-effectiveness, both in initial investment and maintenance. Moreover, the wafer design ensures bidirectional flow, which means it can shut off fluid flow from either direction, a feature enhancing its versatility in various piping systems.
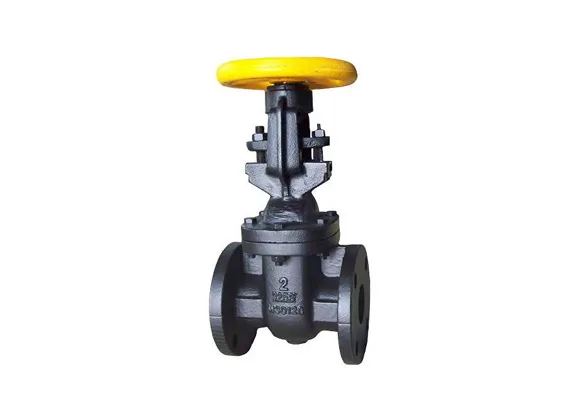
On the other hand, the lugged butterfly valve offers a more robust solution, especially in systems requiring frequent disassembly or partial dismantling for maintenance. This valve features threaded inserts, or lugs, on the outside of the valve body. These lugs enable the valve to be installed in a rigid section of pipe, much like a traditional gate valve. It can also serve as a dead-end service without the downstream piping attached. This feature significantly enhances maintenance flexibility and convenience, as it allows for sections of a piping system to be isolated for repair without affecting the entire system's functionality.
Experience in the field consistently shows that the choice between wafer and lugged butterfly valves hinges on specific operational needs. Systems that demand frequent maintenance access or involve extreme conditions often benefit from the durability and flexibility of lugged valves. Conversely, when cost and space constraints dictate, wafer valves offer a compelling solution.
wafer and lugged butterfly valve
Specialists in fluid dynamics and piping systems emphasize the importance of material selection for these valves. Typical materials include stainless steel, ductile iron, and PVC, each providing varying levels of corrosion resistance and pressure tolerance. For example, in corrosive environments, stainless steel valves are preferred for their resilience against chemical degradation, whereas ductile iron might be selected for its strength and durability in more neutral conditions.
Professionally, manufacturers heighten their offerings by adhering to international standards such as ANSI, API, and ISO, which ensure that products meet global regulatory requirements and compatibility needs. This commitment to quality and standardization enhances the overall trustworthiness of wafer and lugged butterfly valves within industrial applications.
In advising clients or peers, it’s crucial to perform a thorough assessment of system needs, considering factors such as pressure, temperature, and fluid properties, alongside maintenance schedules and ecological considerations. This ensures the selection of a valve that not only meets immediate operational needs but also contributes to the long-term sustainability and efficiency of the system.
Innovations in valve technology continue to evolve, with advancements focusing on enhancing sealing technologies, automation capabilities, and material resilience, thus broadening the scope and efficiency of wafer and lugged butterfly valves. These enhancements are pivotal for industries striving to achieve operational excellence and environmental responsibility.
Ultimately, the wafer and lugged butterfly valves are indispensable in contemporary industrial applications. Their flexibility, economic advantages, and adaptability position them as critical assets in fluid management systems. As industries advance, the role of these valves will likely expand, with emphasis on enhancing their operational scope and efficacy without compromising on safety and environmental standards.