Feb . 14, 2025 13:56
Butterfly valves have cemented their reputation as an essential component within various piping systems due to their simplicity, efficiency, and economic value. Engineers and technicians explore three primary types of butterfly valves to strive for their specific requirements and applications concentric (centric), double-offset (high-performance), and triple-offset (triple-eccentric) designs. Each type bears distinct features ideal for particular conditions, leading to an evolving landscape for these components in industrial and mechanical engineering fields.
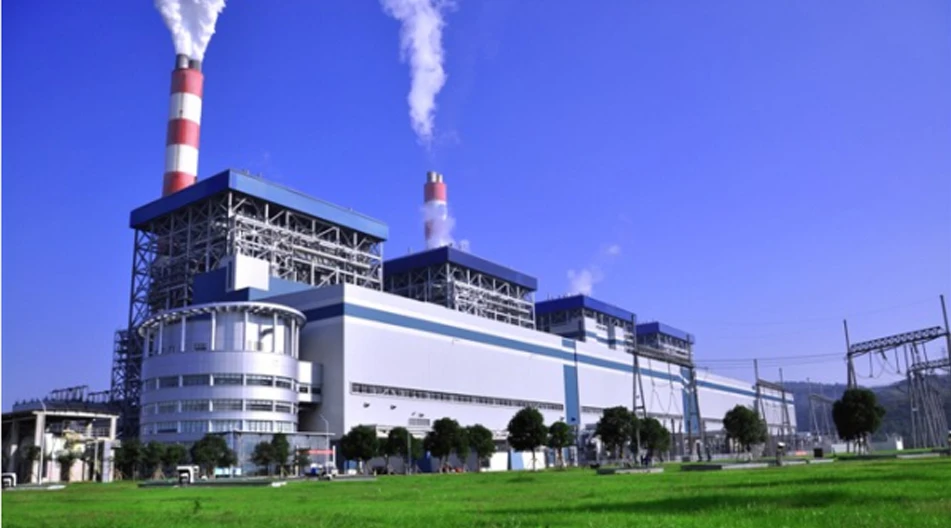
Concentric Butterfly Valves, or zero-offset butterfly valves, exhibit a straightforward configuration where the disc is concentrically aligned with the valve body, positioning it in the center. As the initial design within the genre, concentric valves primarily operate with a rubber-lined seat. This alignment allows the valve to open and close with minimal resistance as the rubber material ensures a tight seal, minimizing potential leakage when the valve is closed. Widely used in low-pressure and low-temperature situations, concentric butterfly valves are typically employed in water distribution systems, HVAC, and applications where moderate sealing suffices. While they are cost-efficient and maintain a compact design, concentric butterfly valves might not be the go-to choice for scenarios demanding high-pressure tolerance or excess corrosion resistance.
Venturing into more sophisticated territories, Double-Offset Butterfly Valves, also recognized as high-performance valves, address the limitations observed in their concentric counterparts. By setting the shaft slightly behind the disc and away from the valve centerline, engineers introduced the first offset, while the second offset displaces the shaft from the pipe or valve centerline. These modifications minimize friction and wear between the valve seat and disc—enabling the use of materials like metal-to-metal seating arrangements. Double-offset valves are preferable in systems operating under higher pressures and temperatures, such as in refineries and industrial process plants. Apart from enabling better longevity against wear, the enhanced sealing mechanics afford these valves added utility in throttling applications, wherein precise flow regulation is imperative.
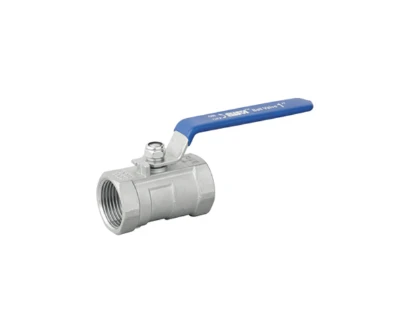
Taking the pursuit of resilience and precision up several notches, Triple-Offset Butterfly Valves (TOVs) are synonymous with demands for absolutely zero leakage in highly critical applications. The third offset in these valves introduces an inclined cone axis of the disc, effectively eliminating sliding contact between the seat and seal until closure is reached. This triple-offset configuration establishes a conical sealing surface, allowing for a torque-seated, reliable barrier without the elastic deformations conventional in lesser designs. Primarily manufactured using robust metals for both the seat and disc, TOVs are ideal in extreme environments, including high-pressure hydrocarbon processing, cryogenic applications, and within the chemical industry. In situations where safety and efficiency are priority, particularly where fugitive emissions could be detrimental, TOV experiences consistently reiterate the pivotal role they play.
what are the three types of butterfly valves
Understanding the spectrum of butterfly valve types is invaluable for selecting precision equipment that aligns with operational needs. Engineers and procurement specialists are armed with the capacity to evaluate cost versus performance while considering media compatibility and the environmental parameters of their applications. The choice between concentric, double-offset, and triple-offset valves hinges on several factors ranging from installation conditions to long-term maintenance commitments. As these elements weave into a decision-making matrix, consulting seasoned experts and leveraging empirical field data enhances both competency and confidence in selection.
The versatility offered by these valve types continues to expand, innovating in fields where energy efficiency, minimized environmental impact, and operational safety command unwavering focus. As manufacturers advance materials and design, new evolutions in butterfly valve technology will possibly manifest, accommodating even higher temperatures, rigorous pressure environments, and exceptional precision control—cornerstones for tomorrow’s engineering challenges.
In synthesizing industry-driven experiences with technological breakthroughs, butterfly valves will remain indispensable tools for engineers striving for exceptional performance and sustainable solutions. Their role as gatekeepers in the fluid and gas handling domain is set to evolve in sync with the ever-changing demands of the global market, where quality, reliability, and seamless operation define success.